Introduction
The maritime industry is also evolving to fight climate change and global warming. One way of doing this has been to research and implement renewable energy sources to propel and power ships. Wind propulsion systems are an option among several others to reduce dependency on fossil fuels and associated emissions.
While this technology has been successfully implemented in smaller vessels, widespread adoption remains a challenge due to the high power demands of large vessels. In this article, we explore the different wind propulsion solutions that are available and enumerate possible solutions to the unique challenges offered by this technology.
What are wind propulsion systems?
Wind propulsion systems are systems that harness the power of wind energy to move a ship. The primary means of doing this is to rig up sails that catch winds and move the ship along the direction of the wind. This is the most direct means of harnessing wind energy.
IC engines are now more reliable than ever before. However, the increase in carbon dioxide and greenhouse gas emissions from the shipping industry has contributed to climate issues such as ozone depletion, global warming, and rising sea levels. As a result, research is underway to commercialize clean renewable energy sources for shipping.
Wind-powered ships have emerged as a possible solution as they have served us well for several centuries for maritime transportation. However, its application for commercial ships has some challenges that need appropriate solutions. But before we delve into that, let us explore the different solutions that are currently available in the market for wind propulsion technology.
Types of wind-assisted propulsion systems
Several systems and equipment have been designed over the years to harness wind energy. However, only a few have survived implementation and testing. In this section, we shall look at four such systems that have the potential for use in commercial shipping.
Ventilated foil system
The ventilated foil system uses aeronautic technology to generate high thrust from wind. It uses the concept of boundary layer suction to generate high propelling force relative to its size.

Ventilated foil system onboard MV Frisian Sea. Photo by Joop Klaasman
This system can reduce a ship’s fuel consumption by 10-30 percent depending on the weather. Optimal weather routing can increase fuel savings. The system can be fitted in two days and comes in fixed and foldable designs. The foldable designs allow the vessel to carry out cargo operations without any hindrance.
Trials carried out since 2021 show that it is possible to recover the costs of the ventilated foil system within about four years of installation through reduced fuel costs. The system is fully automated and uses a suction wing to increase propulsion power.
Kite sails
Kite sails use literal kites to generate thrust from the wind and move a ship. These kites can go up to an altitude of 500 m and save up to 40% fuel as was noticed in the case of MV Theseus. The fuel savings are higher at higher ship speeds.
An advantage of kite sails over wing sails and Flettner rotors is that they neither lift the ship’s center of gravity nor cause any heeling.
There are several companies such as Skysails and Airseas who are actively working to improve the efficiency of kite sails. Kite sails offer pollutant emissions reductions of up to 15% (according to Skysails). They also occupy minimal deck space as the kite can be folded and stored in a small area when not in use.
Wing sails
Wing sails have the shape of airplane wings to achieve thrust the same way as an airplane achieves lift. Several of these are fitted along the open deck. Their position can be automated like the ventilated foil system to adapt to changing wind speed and direction for maximum thrust.
The wing sails have a superior drag/lift performance ratio and can fold to a quarter of their length for overhead clearance or during bad weather. The wing sails work better with ships that have a large open deck space with limited deck machinery and accommodation.
They offer fuel savings and emissions reductions of up to 40% (according to Bound4Blue).
Rotor sails
Rotor sails or Flettner rotors are cylinder-shaped sails that generate thrust using the Magnus effect. The cylinders are mounted on electric motors. The motors rotate the sails along their height to accelerate wind at the forward side of the cylinder and retard it at the aft side of the cylinder.
This creates a pressure differential between the aft and forward sides of the cylinder and produces thrust perpendicular to the wind direction. The motors come on automatically when the wind direction is appropriate. For maximum thrust, the wind must flow from the port to the starboard or vice versa. The number of rotors that can be mounted depends on the ship’s deck space. Rotor sails can also be folded for overhead clearance or bad weather conditions.
They offer reductions in fuel consumption and pollutant emissions of up to 20% (according to Norsepower).
Overcoming challenges in wind propulsion
Wind propulsion is sustainable, predictable, and inexhaustible. However, several challenges can deter ship owners from investing in wind technologies. Let us take a look at some of the key challenges and their possible solutions.
Varying weather conditions
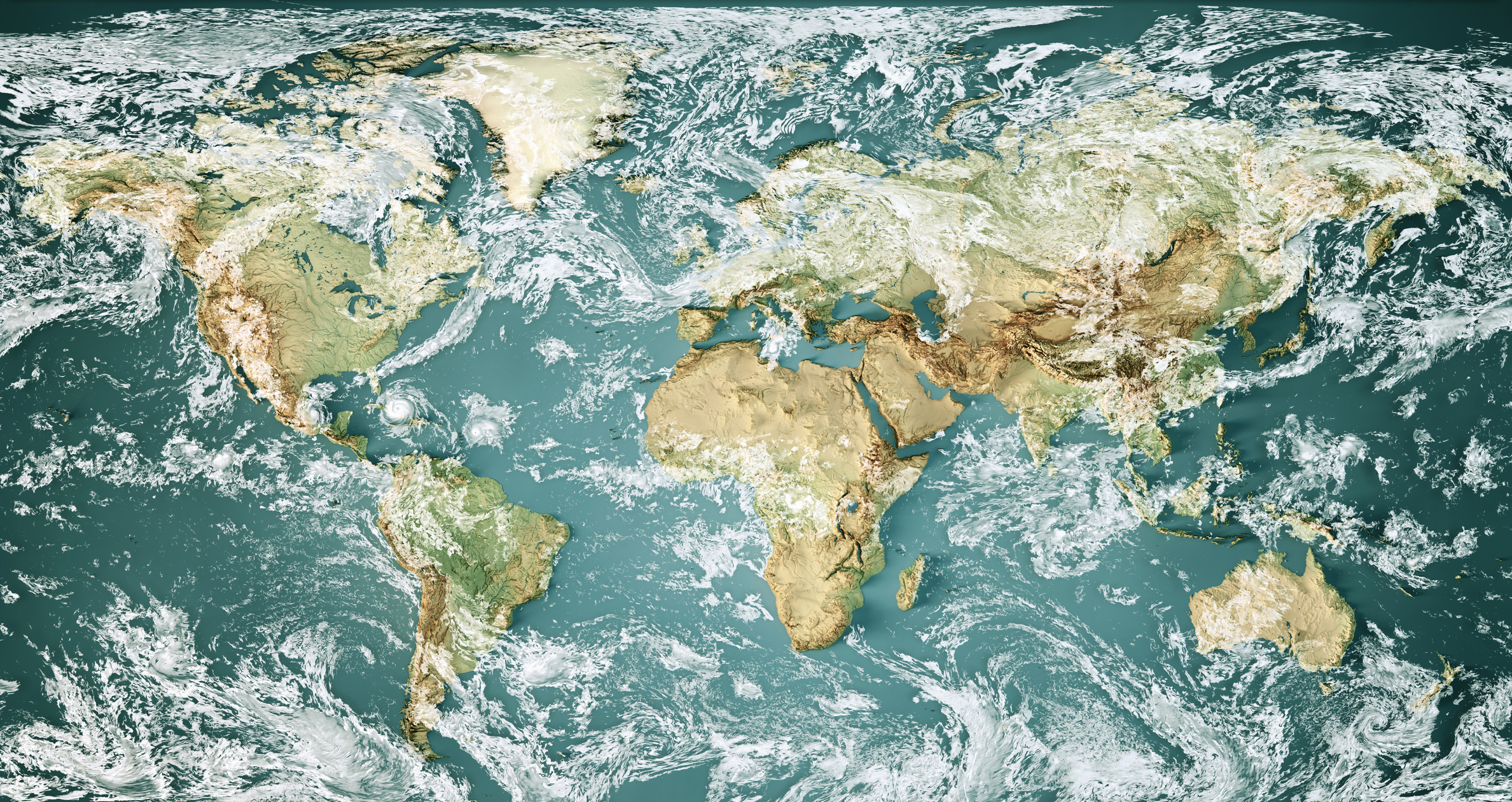
Wind speed and directions varies with location and season across the globe
To depend on wind energy to cross oceans can be daunting given how its speed and direction can vary between two different locations as well as en route. In such cases, inconsistent and unreliable propulsion can discourage a ship owner from depending on wind technologies.
However, advanced weather predictions and routing systems can guide vessels to navigate through areas with favorable wind conditions.
Initial investment cost

The high cost of initial investment for retrofitting or integrating wind propulsion systems into existing vessels is a significant obstacle for vessel owners. However, many countries are offering subsidies and financial incentives to balance these costs and encourage ship owners to install wind-assisted propulsion systems.
Adaptability to different vessel types and sizes

All vessels are different and may have compatibility issues with new technology integration.
Different vessels have different operational requirements. For instance, there is no use of the open deck on a Ro-ro vessel but the same cannot be said for container vessels. Wind propulsion solutions will have to tailor themselves to the size and operational requirements of different vessels.
Technological maturity
Many wind-assisted propulsion technologies are still in their early phases and will need some time for standardization and maturity. This may prevent widespread adoption. There is a need for global industry collaboration to set common guidelines and standards for wind propulsion systems Manufacturers, ship owners, and regulators need to work to fulfill this objective.
Crew training and familiarity

Wind propulsion systems will be a new technology that all crew members will be unfamiliar with. To ensure seamless operation and maintenance of a wind propulsion system, extensive training programs will have to be carried out.
Conclusion
Climate change and air pollution have urged the international community to take measures against emissions. MARPOL has released mandatory operational and technical measures that came into effect in 2013. The aim is to reduce the carbon dioxide emissions from the shipping industry by 20% by 2020 and 50% by 2050. This endeavor requires more efficient use of energy and reduced emissions.
Ship operators are actively looking for cleaner fuels, including renewable energy sources to offset their greenhouse gas emissions without affecting operations. Wind propulsion has the potential to transform the current situation at all levels and in appreciable magnitudes. It may be retrofitted into existing ships or added to newbuilds for maximum output and synergy.